Crystalline Silica
What is crystalline silica?
Crystalline silica is a basic component of soil, sand, granite, and other minerals, the most common form being quartz. All forms of crystalline silica are at risk of turning into respirable size particles when workers chip, cut, drill, or grind objects. It can be found in sand, stone, and soil, as well as concrete, brick, mortars, and other common construction materials. However as OSHA cracks down on crystalline silica exposure, increasing fines and implementing harsh penalties in an effort to protect workers, more and more companies in the construction and blasting abrasives industries are switching over to clean, safe, crystalline silica-free options.
Natural Materials Containing Crystalline Silica:
- sand
- soil and rock
- gravel
- sandstone, slate, and granite
- clay
Common Construction Materials Composed of Crystalline Silica:
- ceramic and terracotta tiles
- concrete and concrete blocks
- manufactured stone
- roof tiles
- bricks and blocks
- grouts and mortar
- abrasive materials
NOTE: SiONEER glass products are made from 100% recycled glass which is amorphous silica. Amorphous silica is harmless to humans when used in construction & industrial applications.
What happens when you inhale crystalline silica dust?
Inhaling crystalline silica dust can cause silicosis, a slow developing chronic disease that ruin a person’s ability to breathe. It is characterized by shortness of breath, fever, and cyanosis (bluish skin). Silicosis can be both debilitating and fatal. As crystalline silica dust swarms from cutting, drilling, or blasting, small particles are inhaled by workers. The particles flow deep into the lungs and interfere with oxygen getting into the bloodstream. Silicosis can damage the kidneys, impair the immune system’s ability to ward off infection, and ultimately lead to death.
Furthermore, crystalline silica dust has been classified as a human lung carcinogen by both the International Agency for Research on Cancer (IARC) and the US National Toxicology Program (NTP), and is recognized by the National Cancer Institute as causing increased rates of lung cancer in exposed workers. It can also lead to an increased risk of developing COPD (Chronic Obstructive Pulmonary Disease) and Pulmonary Tuberculosis.
Workers in the blasting abrasives industry who inhale crystalline silica particles are at an increased risk of developing:
- COPD (Chronic Obstructive Pulmonary Disease)
- Kidney Disease
- Lung Cancer
- Pulmonary Tuberculosis
- Silicosis
Why are blasting abrasive workers at an increased risk?
According to the CDC (Centers for Disease Control and Prevention), when workers inhale the crystalline silica used in abrasive blasting, the lung tissue reacts by developing fibrotic nodules and scarring around the trapped silica particles. If the nodules grow too large, breathing becomes difficult and death may result. The silica sand used in abrasive blasting typically fractures into fine particles and becomes airborne. Inhalation produces a more severe lung reaction than silica that is not freshly fractured. This factor may contribute to the development of acute and accelerated forms of silicosis among sandblasters.
What are the alternatives to using crystalline silica in both blasting abrasives and the construction industry in general?
Alternative, less toxic blasting materials include ice cubes, plastic bead media, ground biodegradable materials like walnut shells or corn cob, high pressure water, and of course, SiONEER recycled glass products! Finely ground, sanitized, and treated glass at size 40/70 mesh makes for a durable and aggressive blasting media that produces less dust and no contaminants.
For the construction industry, glass powder makes for a highly reactive pozzolan alternative to fly ash, various toxic slags, and silica sand – and out performs all three. When SiONEER glass pozzolan is added to a concrete mix it results in ultra high-strength 100 year concrete. Other benefits include enhanced durability, chlorine permeability, decreased health risk to workers, and the suppression of ASR.
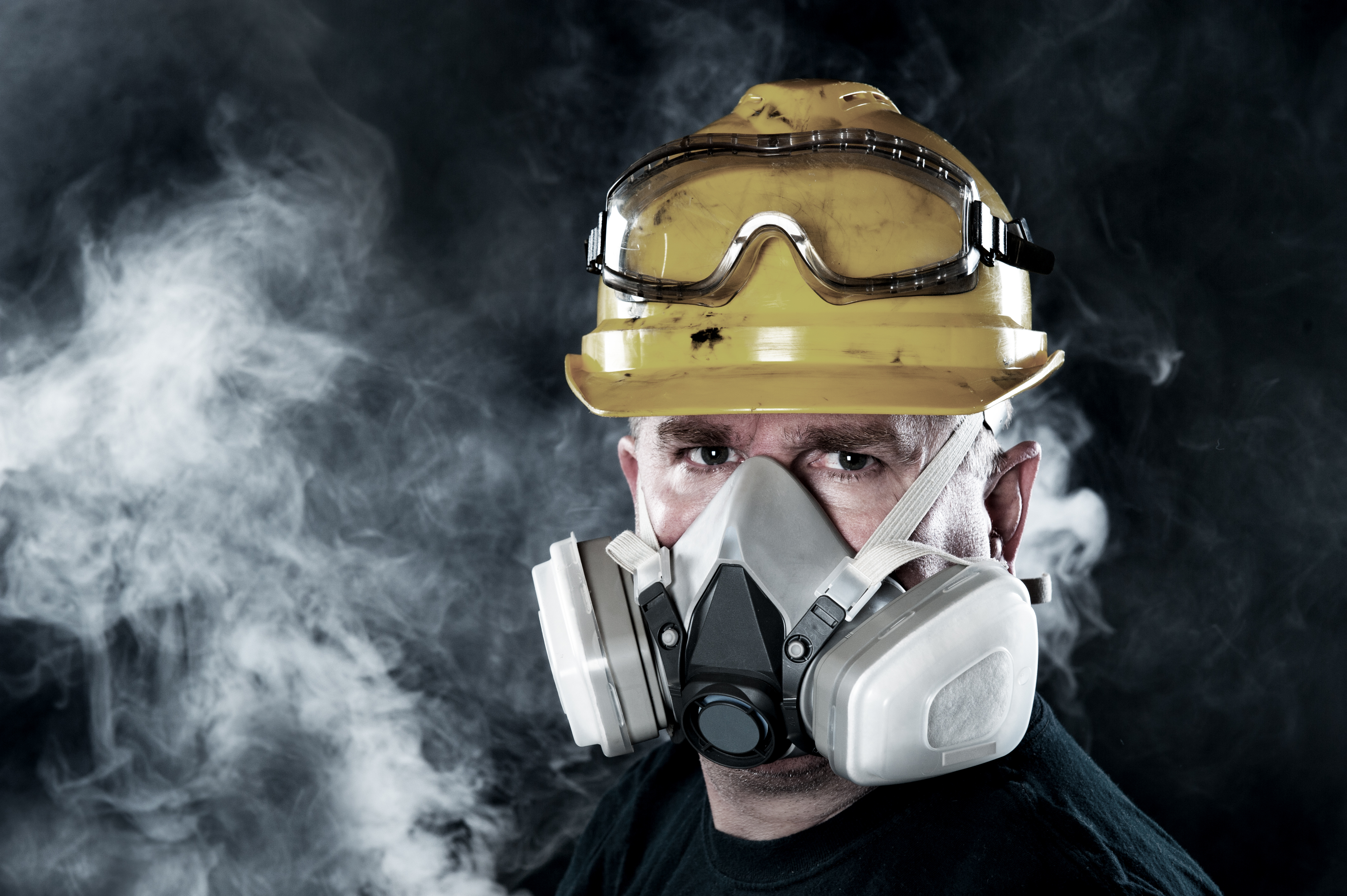