Materials Spotlight
SiONEER President and CEO, Doug Jackson, was recently interviewed by stok, an integrated real estate services firm that provides sustainable design, project management, and engineering & commissioning services. Focusing on environmentally restorative and socially equitable projects, stok featured Sioneer in its Materials Spotlight highlighting healthy building. stok has partnered with reputable clients like Google, Amazon, and Facebook.
Read the excerpt from stok below, or the full article here.
MATERIALS SPOTLIGHT: RECYCLED GLASS IN CONCRETE
By: stok
The carbon impacts associated with the production of portland cement is not a new sustainability issue. But there is a new solution.
We sat down with Doug Jackson, President & CEO of SiONEER, a glass processing company that’s bringing a new product to market aimed at tackling the issue.
A Bit of Background
The common concrete mix is comprised of aggregate, water, sand, various chemical admixtures, and portland cement. The primary function of portland cement in the mix design is to create a binding agent which allows these various ingredients to become concrete.
The manufacturing of portland cement is highly carbon intensive, responsible for roughly 5% of global anthropogenic carbon emissions. It’s commonly substituted, at varying percentages, with fly ash and ground-granulated blast-furnace slag for increased performance and environmental benefit.
However, while fly ash and slag are more sustainable alternatives than utilizing 100% portland cement, they are not perfect solutions. Both are by-products of coal-powered electricity generation, thus procurement is an indirect support of a carbon intensive industry. Additionally, they contain heavy metals that cause adverse health and environmental impacts.
The North American supply of fly ash and slag is also on the decline, resulting in product price and quality inconsistencies. These materials are now being imported and shipped thousands of miles to end up in U.S. concrete, only adding to the carbon impacts of a material we rely so heavily on.
stok: So, what’s the solution?
Doug Jackson: Our pozzolan product is helping to solve not only one, but two environmental issues. According to the U.S. EPA, 75% of glass each year is landfilled due to overwhelming volume and ineffective glass processing. SiONEER takes recycled glass, and sanitizes and pulverizes it, creating a reactive pozzolan end product. This pozzolan has a variety of uses, the primary one being: a portland cement replacement that’s made from 100% post-consumer recycled content, is non-toxic, and results in ultra-high strength concrete.
stok: Beyond sustainability attributes, what are the key benefits of using glass pozzolan in lieu of fly ash or slag?
Doug Jackson: There are two main benefits. First, concrete mix designs can achieve a greater compressive strength. And second, due to the chemical composition of the glass pozzolan – amorphous silica – it mitigates the occurrence of Alkali-Silica Reaction (ASR), a chemical reaction that causes cracking in typical concrete mixes.
Have you ever wondered why the Roman Colosseum has lasted thousands of years while more modern roads and bridges haven’t? The Romans used volcanic ash to make their concrete. Volcanic ash is also amorphous silica – just like Sioneer’s glass pozzolan. The result is ultra-high strength concrete that doesn’t crack, making it last much longer.
stok: There are three U.S. glass pozzolan suppliers, what’s different about your product?
Doug Jackson: There are three different proprietary steps in our manufacturing process. First, is the cleaning process – how paper, garbage, et. cetera is effectively and efficiently separated from the glass. The second is how the glass pozzolan is treated to make it more reactive in the concrete mix, which allows it to gain compressive strength faster. And finally, Sioneer’s equipment can grind the glass into a multitude of sizes, which allows the material to have a variety of use cases beyond glass pozzolan in concrete.
stok: What’s the biggest barrier to widespread market adoption?
Doug Jackson: The biggest barrier for glass pozzolan use in concrete mix is lack of awareness. The use of fly ash and slag has become industry standard, so introducing a new portland cement alternative is difficult. Engineers need to get comfortable enough with the material to specify it, and then the contractor needs to be comfortable enough to communicate the ask to their concrete installation subcontractors and ready-mix suppliers. There is a chain of education that needs to occur in these early use stages.
The driver for use on projects to date has been from the owner, primarily due to alignment with corporate sustainability goals. We’re excited that key innovators like Google and Facebook are working with Sioneer to pilot glass pozzolan on their Silicon Valley development projects. As leaders continue to realize the benefits of using our product over traditional portland cement and its alternatives, we see it catching on industry wide.
Key industry collaborators are working to develop an ASTM standard for glass pozzolan use in concrete mix designs, which will solidify legitimacy of use and mitigate concerns with risk. The standard will be officially published later this year.
Continue reading the full article here.
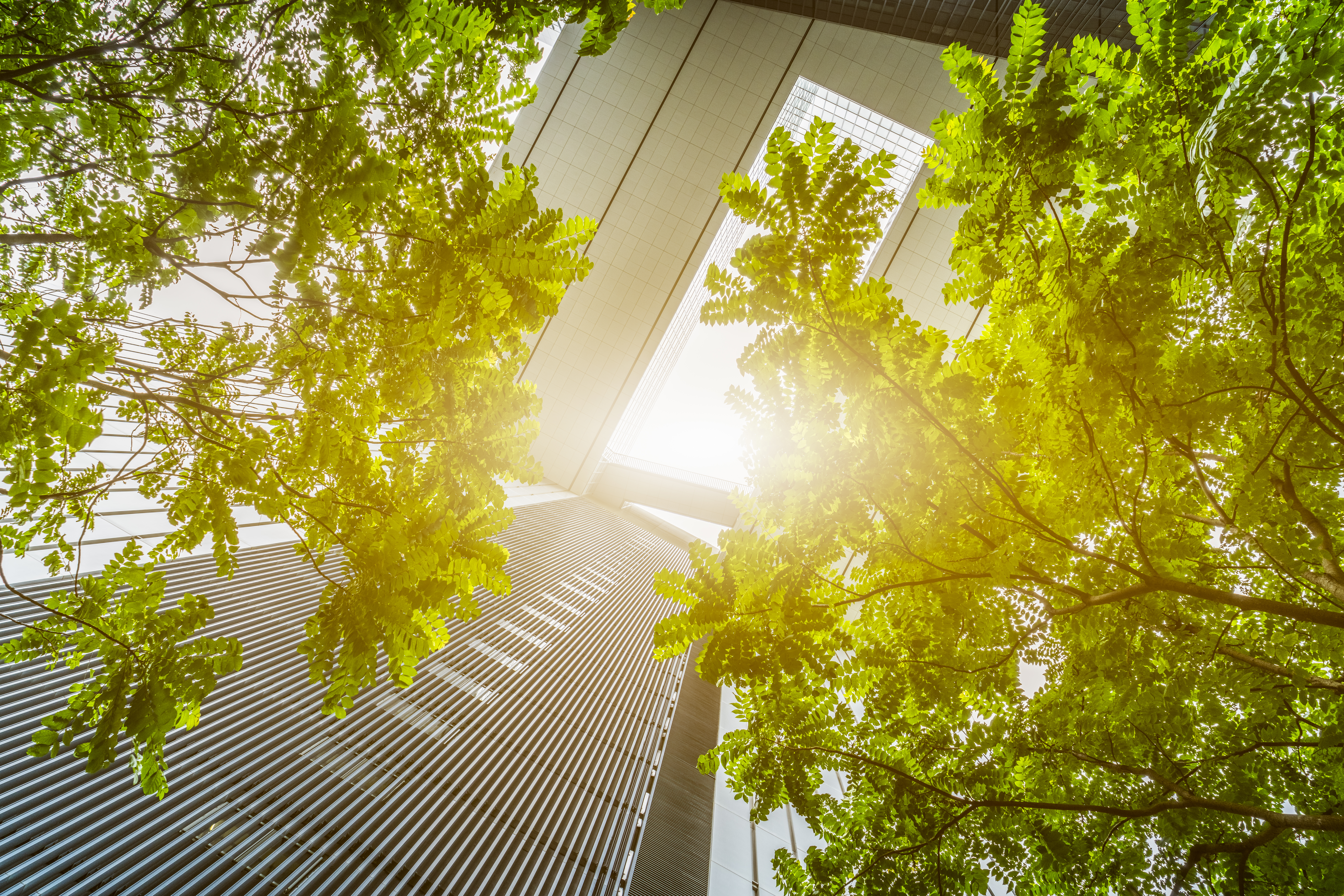